Shandong Zhihua Pipe Industry Co., Ltd.
Improving the corrosion resistance of grooved pipe reducers involves several strategies and considerations. Here are some steps to enhance the corrosion resistance of these components:
Select Corrosion-Resistant Materials:
Choose materials known for their corrosion resistance, such as stainless steel (particularly grades like 316L or 304L), when manufacturing grooved pipe reducers.
Consider the specific environment and the types of chemicals or substances the pipe will be exposed to when selecting the material. Some environments may require higher grades of stainless steel or other specialized materials.
Use Coatings or Linings:
Apply corrosion-resistant coatings or linings to the interior and exterior surfaces of the grooved pipe reducers. Common coatings include epoxy, fusion-bonded epoxy (FBE), or polyethylene coatings.
The choice of coating should be compatible with the material being transported and the operating conditions.
Corrosion Inhibitors:
Use corrosion inhibitors within the fluid being transported to reduce the likelihood of corrosion. These additives can help protect the interior of the pipe and fittings.
Ensure that the chosen corrosion inhibitor is compatible with the pipe material and the fluid being conveyed.
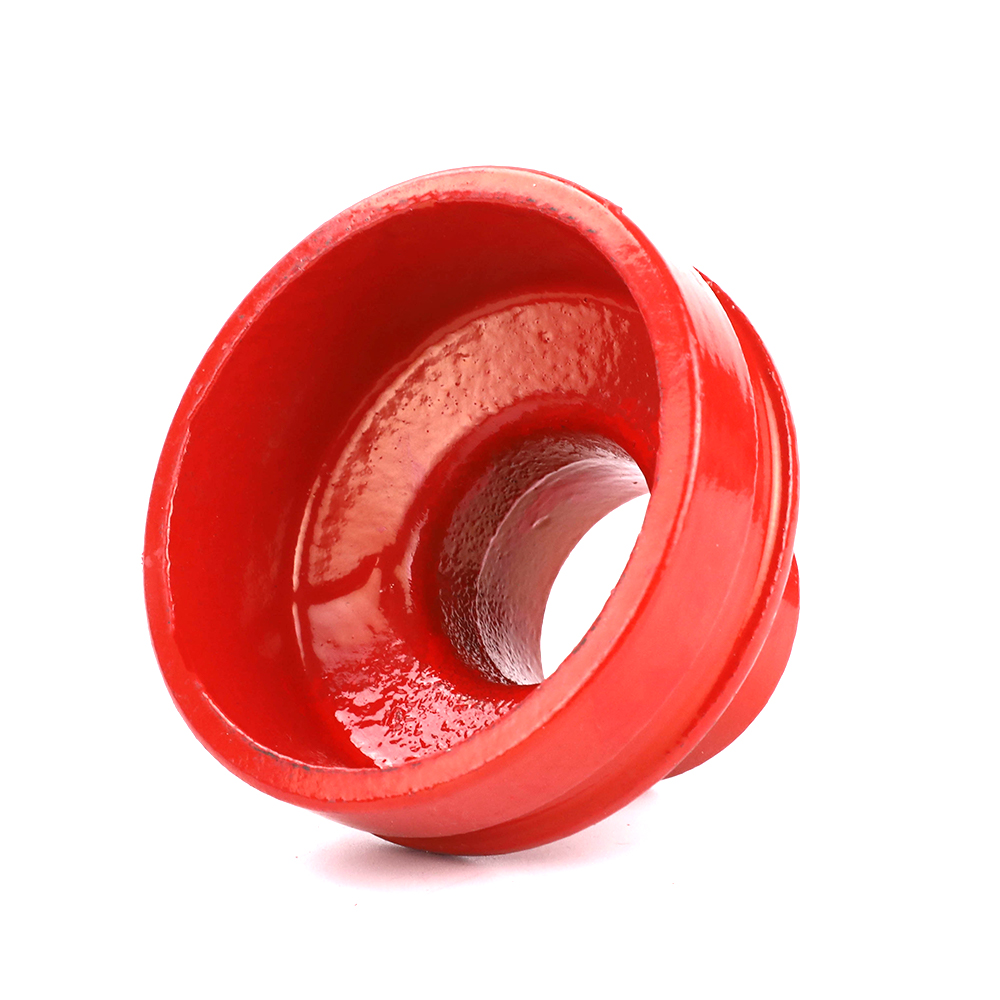
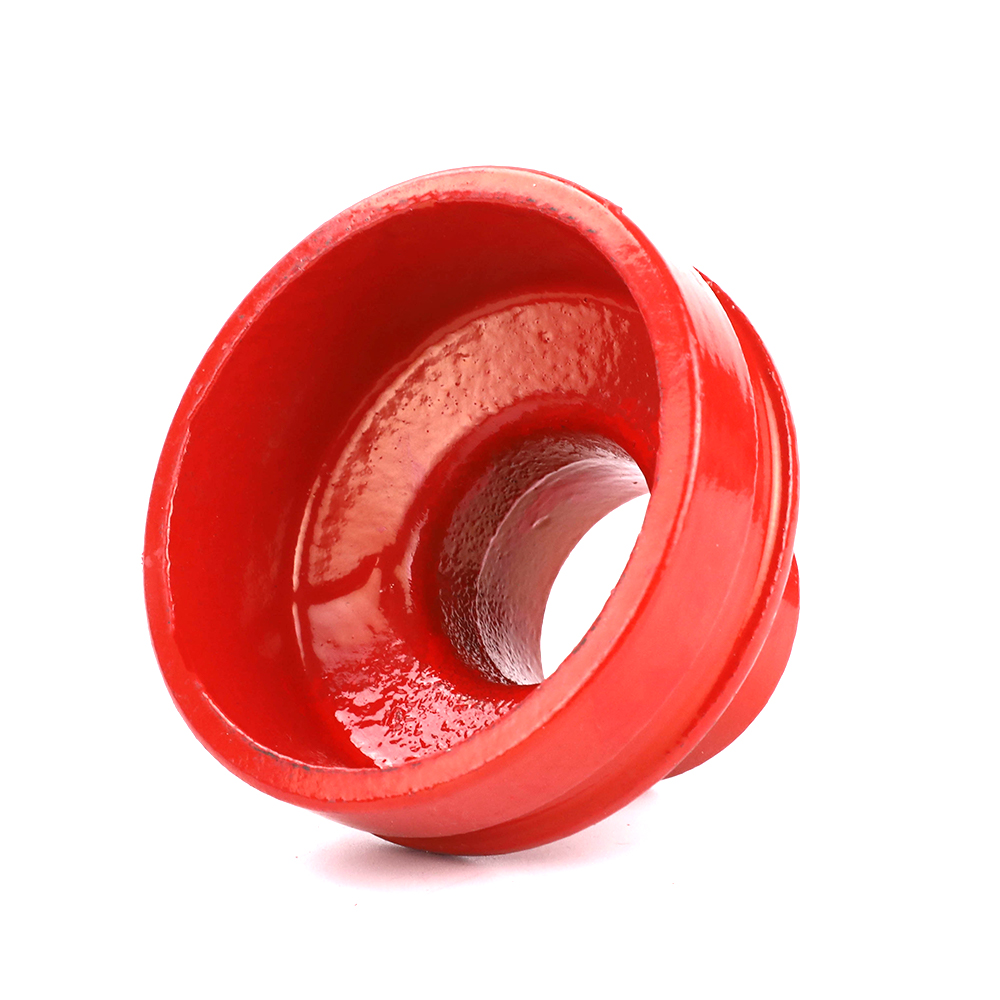
Proper Installation:
Ensure that the grooved pipe reducers are installed correctly and securely. Proper installation helps maintain the integrity of the sealing gasket and prevents moisture or corrosive substances from entering the joint.
Avoid Direct Contact with Corrosive Substances:
Whenever possible, avoid direct contact between the grooved pipe reducers and highly corrosive substances by using compatible piping materials, such as plastic liners or sleeves, where necessary.
Regular Inspection and Maintenance:
Establish a routine inspection and maintenance schedule to monitor the condition of grooved pipe reducers and identify any signs of corrosion early.
Promptly replace any corroded or damaged components to prevent further deterioration and potential leaks.
Proper Cleaning Procedures:
If the grooved pipe system is exposed to corrosive substances or contaminants, implement regular cleaning procedures to remove residue and prevent corrosion buildup.
Cathodic Protection:
Consider the use of cathodic protection systems, such as sacrificial anodes or impressed current systems, in environments where galvanic corrosion is a concern. These systems help divert corrosion away from the grooved pipe reducers.
Environmental Controls:
Implement environmental controls to limit exposure to corrosive elements, such as maintaining proper temperature and humidity levels.
Monitor pH Levels:
Keep an eye on the pH levels of the fluid being transported. Extreme pH levels can accelerate corrosion. Ensure that the fluid chemistry is compatible with the pipe material.